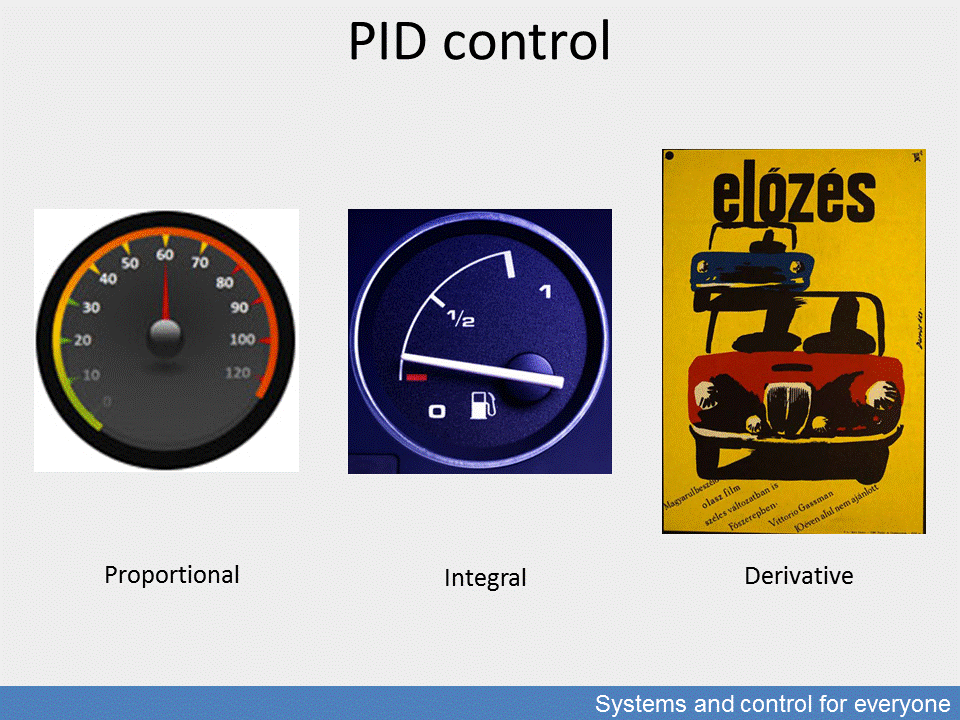
Proportional–Integral–Derivative or PID controllers are the most commonly used control solutions in industrial control systems where a combination of proportional, integral and derivative values of the error signal is applied as the actuating control signal. The integral part improves the static accuracy, while the derivative part accelerates the control system. Naturally, this control often requires a more sophisticated tuning than in the case of the simple try-and-see applications, as the requirements must be precisely coordinated to ensure stability and an acceptable compromise between other requirements of the closed-loop control.
The parameters of the controller are set up on the basis of the process model, in line with the relevant quality requirements. There are several design methods and rules of thumb for tuning the parameters.