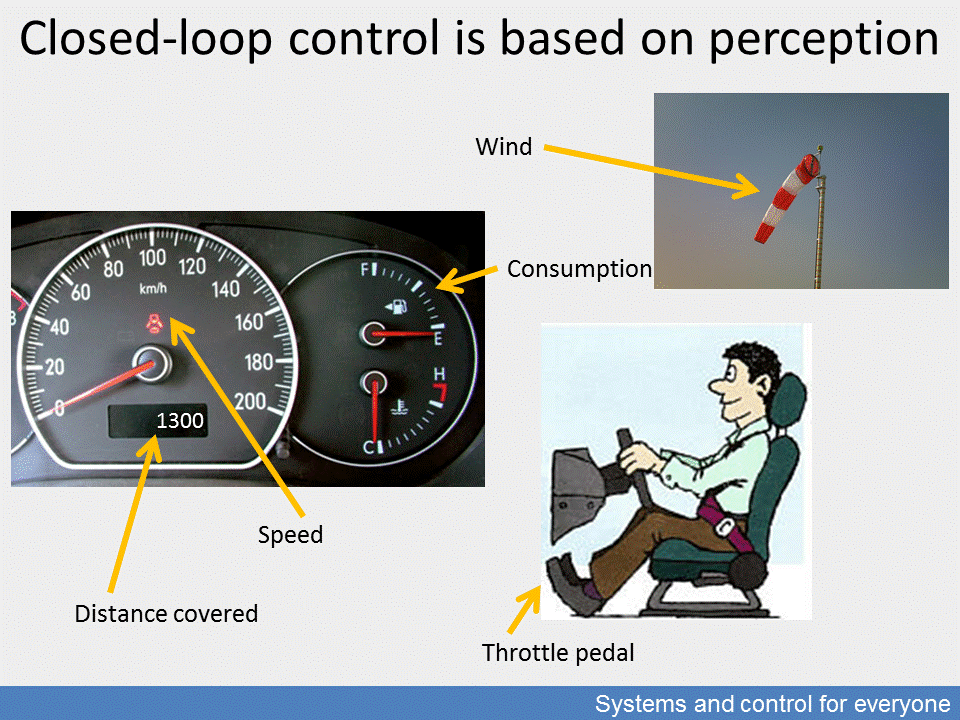
The basic structure of closed-loop control is negative feedback. We measure the output signal of the controlled system and then compare this value with the desired reference signal. On the basis of the difference (error signal), we manipulate the system by modifying its manipulating signal through the controller. Naturally, the dynamics of the process influences the dynamics of setting the desired value of the controlled output signal. Irrespective of the effect which triggered the error signal, the negative feedback ensures that the output signal returns to the desired value after a certain period of time. The controller must be designed to ensure the stability of the control loop and its compliance with the prescribed static and dynamic requirements, while satisfying the given restrictions.
In order for the closed-loop control to take action, an error signal is needed. If there are major delays and dead times in the system, it will take more time to follow the reference signal and eliminate the effect of the disturbances.
If in addition to the output signal, there are other signals that can be measured (disturbances or internal state variables), this information can be used by altering the basic control structure to improve the operation of the closed-loop control process. The more information is available, the better and more prudent decisions can be made.
If the disturbance signal can be measured, the basic structure can be extended with so-called feedforward (disturbance compensation). If internal signals within the process can also be measured, we can create a control circuit which is based on multiple nested negative feedbacks. This is called cascade closed-loop control. If all internal variables (state variables) can be measured, by feeding them back to the system we can create a so-called state feedback control.
When designing the closed-loop control, the model of the controlled system (process) must be considered. The controller must be adapted to the process model and to the quality requirements.
Internal Model Control (IMC) is an effective control structure designed to ensure compliance with the reference signal by means of a controller connected in series with the process in the forward path, while disturbances are suppressed using the negative feedback taken from the difference of the outputs of the process and its model.
When designing closed-loop controls, it is advisable to consider whether other signals are available in addition to the output signal. If so, we have to determine the structure of the closed-loop control, and then design the controller and specify its parameters.
When designing the controller, we often have to consider several aspects and rules. An “optimal” closed-loop control is usually achieved through a compromise.