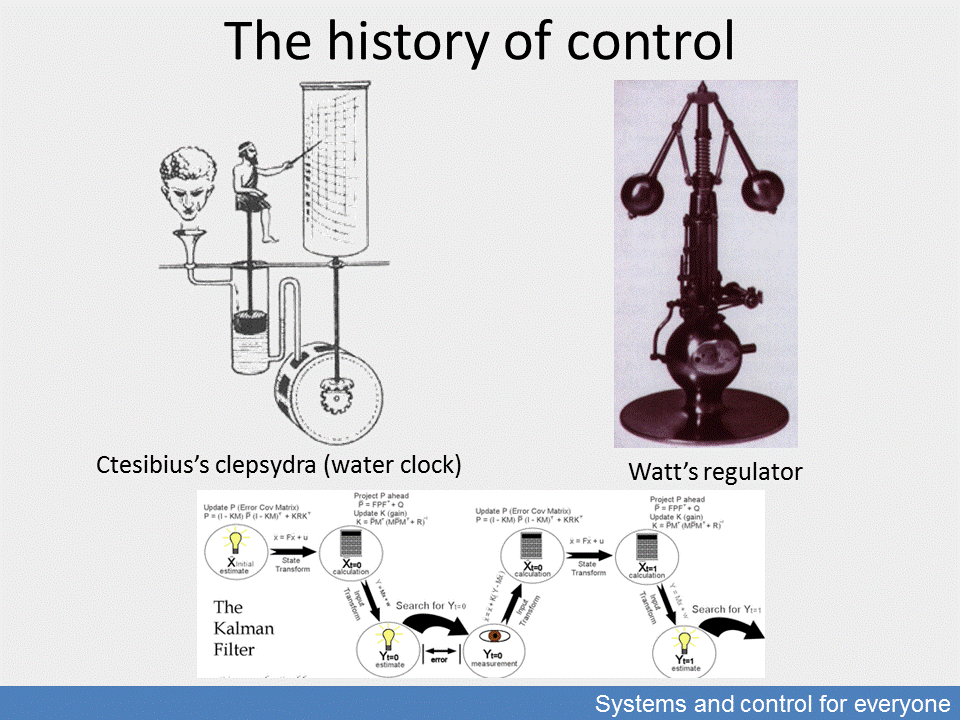
To provide a suitable ending for our introduction to the interminable and continuously developing and expanding world of systems, this last chapter briefly outlines the history of control.
Control engineering is a dynamically developing field even today. New devices and technology raise new theoretical questions and open up the way to new and innovative applications. The involvement of negative feedback in processes is not a new principle: the ancient Greeks had already applied it. Looking back on the evolution of control engineering, we can see a few remarkable trends.
The application of negative feedback relates to the solution of engineering tasks. The evolution of control engineering is closely linked to the practical tasks faced by humanity in certain periods of its history, namely the following:
Looking at these periods, it can be established that man first tried to find its place in space and time, then it tried to change its environment and make its life comfortable. The latter effort was greatly facilitated by the emergence of industrial production. Subsequently, man uses communication to stabilise its place and position in society and tries to get into contact with the universe.
The ancient Greeks had already used various self-operating machines (automata). The first such control system was the clepsydra (water clock) invented by Ctesibius in Alexandria (270 BC). The machine used a float to sense the level of the container and keep it at a constant value. If the water level in the container went down, a valve opened and the container was refilled. The constant level ensured the constant quantity of the water flowing out from the container. The water flowed into a second container, which thus was filled in proportion to the time lapsed. Philo of Byzantium (250 BC) also used a float regulator to control the oil level in an oil lamp. Heron of Alexandria (AD 1st century) also used a similar device for controlling levels, pour wine, open temple doors etc.
Arabic engineers used various float control devices between AD 800 and 1200. They even discovered two-state (on-off) controllers.
With the invention of mechanical clocks, float controlled water clocks became obsolete. Later, the principle of control was reinvented in the period of the Industrial Revolution.
Many self-operating devices were invented in the Industrial Revolution. They featured automatic level, temperature, pressure and speed control. Control applications appeared as early as in the 1600s, such as the speed control of windmills, the temperature control of furnaces (Cornelis Drebbel) or pressure control (Papin). The beginning of the Industrial Revolution is marked by the appearance of James Watt’s steam engine (1769). The first industrial control mechanism was Watt’s centrifugal governor which controlled the speed of the steam engine. The position of the governor depends on the speed of the steam engine. The sensor adjusts the position of the steam piston by moving the lever arms, influencing the quantity of the steam flowing into the engine, and thus regulating the speed of the engine.
After the Industrial Revolution, the next major step in the evolution of control engineering was the definition of how control loops can be described mathematically which made it possible to examine the behaviour of control systems from a mathematical perspective.
The invention of the telephone and the application of feedback operational amplifiers for compensating the damping effect during information transfer opened another new chapter in the history of control engineering,
During WW2 many precision control systems were developed: automated air-traffic control systems, radar antenna calibration systems, the control systems of submarines etc. These technologies were later used for industrial production as well.
The emergence of computers heralded a new era in the development of control systems. Computers are not only used as external devices for easier and more meticulous design, but they are integrated into the control loop in real-time applications. The process and the computer controlling it are connected by peripheries, and the manipulating signal is calculated at all sampling times by software and it is fed to the process input. Thus, computers became organic part of the control loop.
Later, industrial robots were designed to perform precision tasks. Robots are automated machines controlled by computers. Robots are often designed to imitate human characteristics, e.g. robot manipulators copy hand movements. Mobile robots are programmed to behave intelligently, for example to recognise and avoid obstacles while moving.
Space research poses another great challenge for control systems. Putting space shuttles and artificial space objects into orbit and ensuring that they reach their destination require highly accurate, adaptive and super safe control systems which capable of learning.
Today, when implementing different control systems, we have to consider the control principles and the joint application and interaction of computers and communication systems (CCC: Control, Computers, Communication). New technological opportunities direct attention to new potential fields of control. The emergence of new miniature sensors and manipulators open up new perspectives for control engineering. Industrial production processes are now increasingly characterised by distributed control systems (DCS) where several coordinated control systems at different locations ensure high production levels. These systems communicate with and instruct each other, and are capable of carrying out coordinated tasks. The hardware and software enabling all this are already available (PLCs, profibus, TCP/IP, industrial network protocols, etc).
Control theory deals with the structure, analysis and synthesis of control systems.
The classical period of control theory (until ~1960) provided the basic principles of the operation, analysis and synthesis closed-loop control systems based on negative feedback.
The modern period of control theory (~1960–1980) laid emphasis on the state variable description of controlled systems and the corresponding design methods.
By today, the focus has shifted to robust and reliable controls which are less sensitive to parameter changes. The control of non-linear systems, the application of intelligent adaptive systems capable of learning, and the application of control systems intensely relying on connectivity through networks open up new perspectives for control engineering.